HDPE pipes have become an integral part of modern infrastructure and industrial landscapes. Their widespread use in diverse sectors, from urban utility systems to industrial processing plants, highlights their significance. This article aims to provide a thorough examination of HDPE pipes, covering all aspects that are crucial for professionals and enthusiasts in the field.
What is HDPE Pipe?
HDPE pipes are constructed from high - density polyethylene, a polymer renowned for its exceptional properties. High density endows it with robust structural integrity, while its toughness enables it to withstand external forces without easily cracking or deforming. Moreover, its chemical corrosion resistance makes it suitable for transporting a wide range of substances, from water to various chemicals.
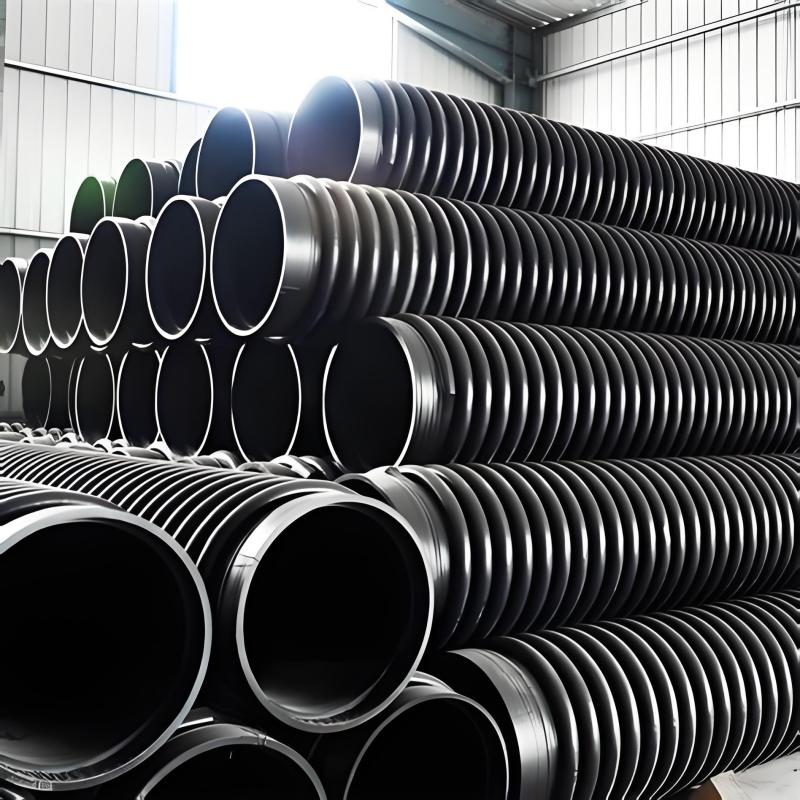
History of HDPE Pipes
Originating in the 1960s, HDPE pipes quickly gained traction in the pipeline manufacturing industry. As engineers and manufacturers recognized its potential, it began to replace traditional materials in many applications. Its superior performance in terms of durability, corrosion resistance, and ease of installation led to its growing popularity over the decades.
What are HDPE pipes used for?
- Municipal Engineering: In urban areas, HDPE pipes are the backbone of water supply and drainage systems. Their corrosion - resistant nature ensures that water remains clean and free from contaminants during transportation. In gas transmission, they can safely carry natural gas over long distances, withstanding high pressures.
- Agricultural Irrigation: Farms rely on HDPE pipes to efficiently distribute water for irrigation. Their UV resistance is a boon in outdoor settings, as they can endure long - term exposure to sunlight without deteriorating. This durability also means they can withstand the rigors of agricultural operations, such as being buried in soil or moved around during field work.
- Mine Drainage: Mines often face the challenge of removing large volumes of water. HDPE pipes are ideal for this task as they can handle the abrasive nature of mine water and the demanding installation conditions in underground or rugged terrains, ensuring a continuous and reliable drainage system.
- Chemical Transportation: The chemical industry requires pipes that can safely transport corrosive substances. HDPE pipes, with their excellent chemical resistance, can carry acids, alkalis, and other chemicals without the risk of leakage or degradation, thus maintaining a high level of safety in chemical processing and transportation.
- Industrial Applications: In industrial facilities, HDPE pipes are used for cooling water circulation and wastewater treatment. Their resistance to corrosion, pressure, and wear allows them to function effectively in harsh industrial environments, where they may be exposed to high - temperature fluids, abrasive particles, or chemical pollutants.
How HDPE pipe is manufactured?
The manufacturing process commences with the selection of high - quality HDPE resin particles. These are fed into an extruder, where high temperature and pressure transform them into a molten, plasticized state. The molten material is then forced through a precisely designed mold, taking the shape of a pipe. After exiting the mold, the newly formed pipe is rapidly cooled, either through spray or immersion cooling methods, to solidify its structure. A sizing device is used to ensure that the pipe's diameter and roundness meet the required standards. Finally, a comprehensive quality inspection is carried out to verify that the pipes are free from defects before they are packaged and shipped.
What are the advantages of HDPE pipes?
- Temperature Resistance: HDPE pipes can endure high - heat environments without losing their structural integrity or softening. In cold regions, they remain flexible and do not become brittle, ensuring consistent performance across a wide temperature range.
- Lightweight: Compared to traditional metal pipes, HDPE pipes are significantly lighter. This not only simplifies transportation but also reduces the cost of installation, as less manpower and equipment are required to handle and install them.
- Flexibility: They possess a certain degree of flexibility, allowing them to be bent slightly to fit around obstacles or conform to the layout of a project site, without compromising their strength.
- Easy Installation: The simplicity of connecting HDPE pipes, through methods like hot melt or electrofusion, reduces the overall construction time and cost. This ease of installation also means that fewer skilled laborers are needed for the job.
- Long Lifespan: Due to their excellent aging resistance, HDPE pipes can serve for many years with minimal maintenance. This long lifespan makes them a cost - effective choice in the long run, as they do not need to be frequently replaced.
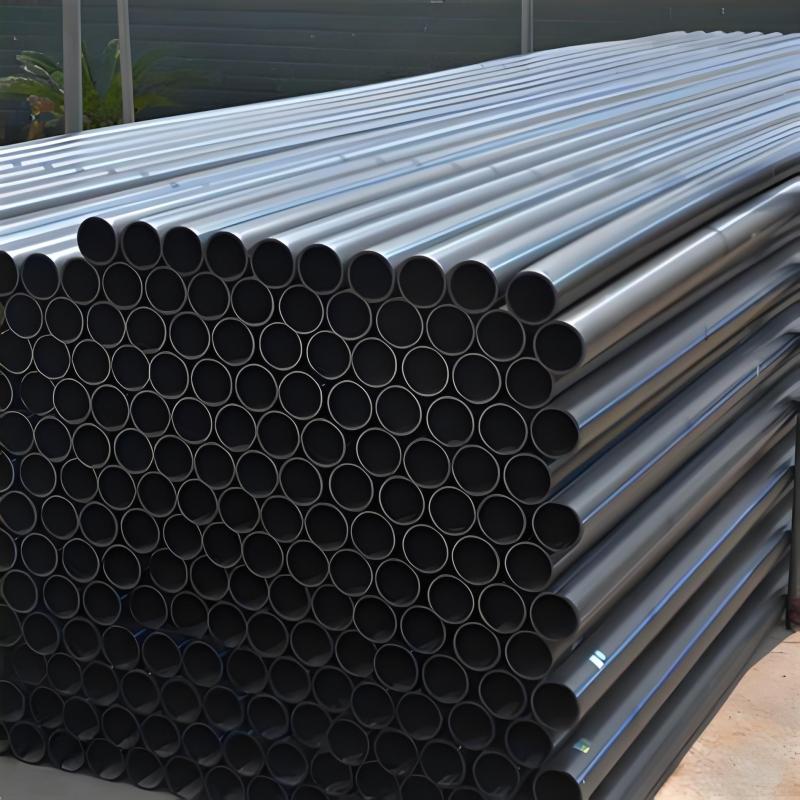
HDPE Pipe Price
The price of HDPE pipes is determined by multiple factors. Pipe specifications, such as diameter and wall thickness, play a significant role. Larger - diameter and thicker - walled pipes are generally more expensive. The quality of the raw materials, brand reputation, production processes, and market supply - demand dynamics also influence the price. Additionally, bulk purchases often come at a lower unit cost. Given the potential price fluctuations, it is advisable for buyers to compare quotes from different suppliers to get the best value for their money.
How to Connect HDPE Pipes?
Common connection methods for HDPE pipes include hot melt connection, which involves heating the pipe ends and connectors to melt and join them. Electrofusion connection is suitable for large - diameter pipes, using electrofusion fittings. Mechanical connection, with the help of clamps or fittings, is useful for temporary or detachable setups. Hot melt butt connection is ideal for long - distance connections, and insertion connection, which uses threaded or other fixing means, is convenient for quick installation and disassembly. When connecting HDPE pipes, it is essential to follow the correct procedures and industry standards to ensure a secure and leak - free connection.
Future Trends of HDPE Pipe Technology
The future of HDPE pipeline technology holds great promise. There will be a greater focus on using sustainable materials to reduce environmental impact. Voltage resistance will be enhanced to expand their use in high - voltage applications. Connection technology will be innovated to improve reliability and sealing. The integration of intelligent technology for remote monitoring and control will increase system efficiency and safety. Moreover, efforts will be made to further improve corrosion resistance for use in even more harsh environments, and their application scope will be broadened to new fields like medical and aerospace.
In conclusion, HDPE pipes, with their remarkable properties, diverse applications, and promising future developments, are set to continue playing a pivotal role in the advancement of infrastructure and industrial sectors. Their versatility and reliability make them a preferred choice for a wide range of projects, and as technology evolves, they are likely to become even more efficient and adaptable.
You are welcome to : phone call, Message, Wechat, Email& Seaching us, etc.